High-Efficiency and Superior Processing Services
KUWAI-LAIN possesses advanced and well-established processing technologies, continuously enhancing and refining through consistent practice. Our in-house equipment includes a range of cutting-edge machines, from 3-axis to 5-axis CNC machines, as well as multi-tasking turning centers, allowing us to flexibly meet various customer processing needs. Whether it's simple part machining or complex high-precision manufacturing, we offer the most suitable solutions.
Moreover, KUWAI-LAIN has an outstanding R&D design team that can provide comprehensive assistance during the initial development stages and support through to mass production. Our team is dedicated to offering timely and effective technical support to ensure that customer needs are quickly addressed and met, helping customers successfully launch high-quality products.
In terms of technical applications, we use a variety of advanced design and processing software, including Solid Edge, Inventor, Edge CAM, and NX CAM. These tools not only enhance our design efficiency but also ensure accuracy in the processing stage. We are committed to exploring and applying the latest technologies to provide higher value-added services to our customers.
Professional Partner for Pre/Post-Processing
Whether it's selecting materials before processing or handling processes after machining, we have established solid partnerships with long-term, high-quality suppliers. In terms of materials, we can provide various premium raw materials, including aluminum alloys, stainless steel, alloy steel, and aluminum extrusion, all of which offer excellent performance in strength, corrosion resistance, and lightweight properties, meeting the needs of customers across different industries.
In post-processing, our partners offer a wide range of services, including anodizing for aluminum, passivation for stainless steel, precious metal plating, chemical nickel plating, powder coating, and heat treatment. These processes not only enhance the aesthetics of the products but also improve their durability and corrosion resistance. We are committed to ensuring that every customer's processing needs are fully met and continually seek innovation and improvement to enhance service quality and customer satisfaction. No matter how specific the customer's requirements are, we will do our utmost to provide the most suitable solutions.
Equipment/Instruments | Brand | Model | X-axis (mm) | Y-axis (mm) | ZX-axis (mm)) | Remarks |
---|---|---|---|---|---|---|
5-Axis Universal Machining Center | DMG MORI | DMU 80 eVo | 800 | 650 | 550 | ※ X, Y axes use linear motor drives B-axis:-5°~110° C-axis:0°~360° |
Multi-tasking Turning Center | DMG MORI | CTX BETA 800 | 300 | 120 | 850 | |
3-Axis Vertical Machining Center | AWEA | AF-1000 | 1020 | 550 | 635 | |
3-Axis Vertical Machining Center - Exchangeable | AWEA | AF-860-APC | 860 | 600 | 600 | |
Precision Lathe | KINWA | CH-430X1100 | 床面上旋徑 432 mm | |||
Precision Grinder | PERFECT | PFG-4080AH | 800 | 400 | - | |
Cutting Machine | - | - | - | - | - | |
Hydraulic Press | - | - | - | - | - | |
Laser Engraving Machine | - | - | - | - | - |
AWEA 3-Axis Vertical Machining Center
DMG 5-Axis Universal Machining Center
DMG Multi-tasking Turning Center
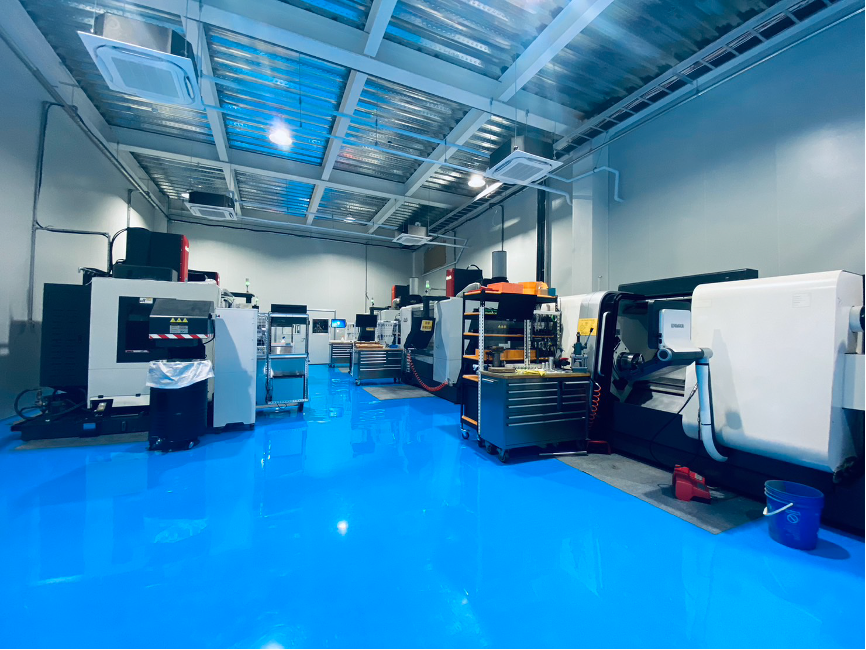
High Quality Begins with Self-Discipline
We firmly believe that maintaining a clean working environment is just as important as delivering excellent product quality to our customers. To achieve this goal, we strictly adhere to the 6S management principles, which emphasize sorting, setting in order, shining, standardizing, sustaining discipline, and safety. This methodology is the cornerstone of our efforts to improve work efficiency. Additionally, we fully implement the AS9100 quality system guidelines, ensuring that our operational environment is always in optimal condition. These efforts not only reduce unnecessary resource consumption but also significantly enhance overall work efficiency, providing customers with more valuable services.
Temperature and Humidity Controlled Processing Environment
In the machining process, temperature and humidity in the environment are key factors that affect machine stability. As such, all of our equipment is housed in a dedicated temperature- and humidity-controlled space. The ambient temperature around our equipment is precisely controlled at 21±3°C, and the humidity is maintained between 40% and 60% RH. This setup ensures that both the machines and personnel operate under the most ideal conditions, thereby improving production efficiency and product quality.
Additionally, our processing equipment is equipped with voltage stabilizers to prevent voltage surges from destabilizing the machine’s power supply, which could impact the normal functioning of the CNC system. These thoughtful measures not only protect our equipment but also ensure we consistently deliver high-quality products and services, giving our customers peace of mind when choosing our solutions.
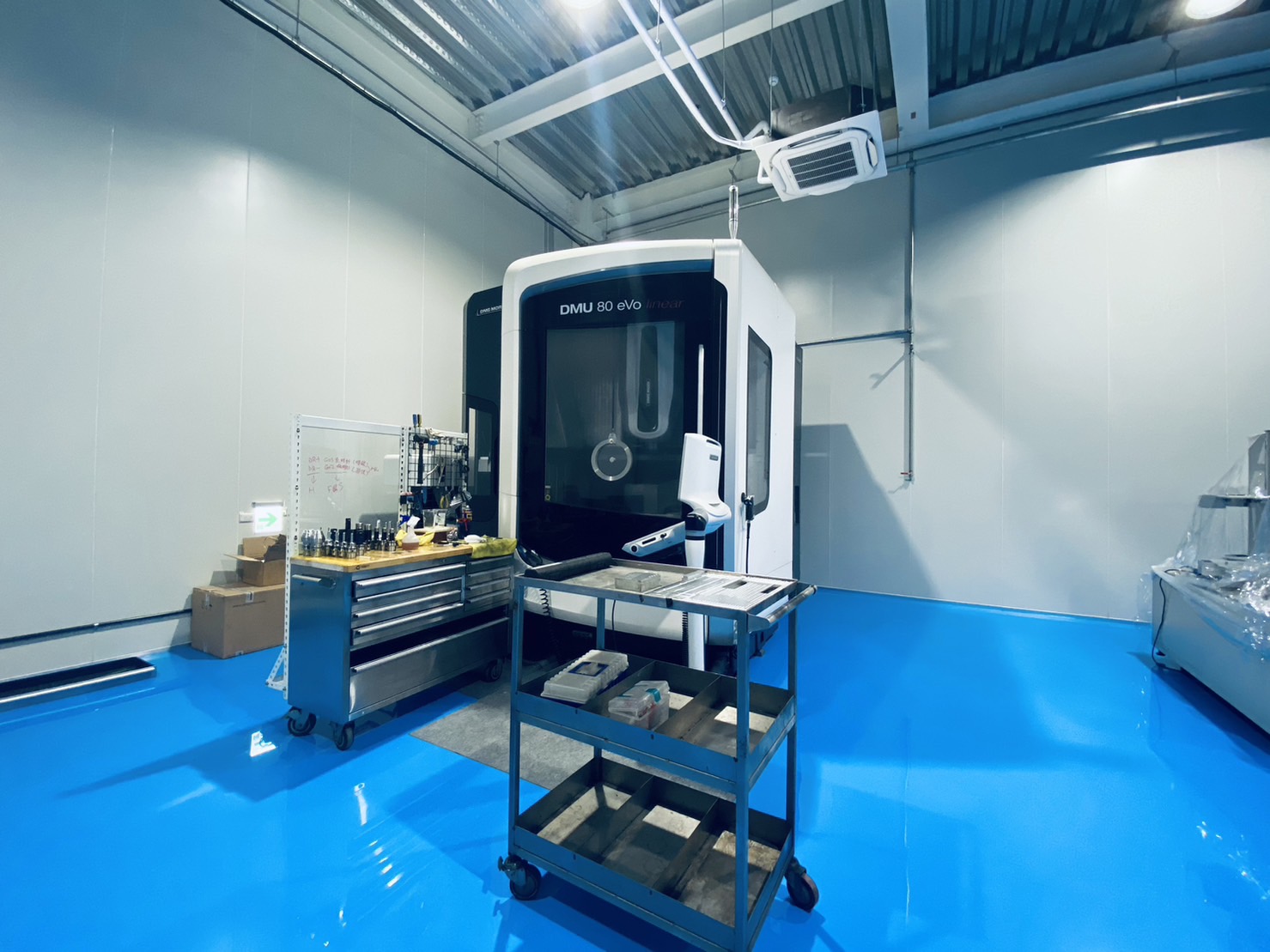